Čekací doby ve výrobě a co s nimi
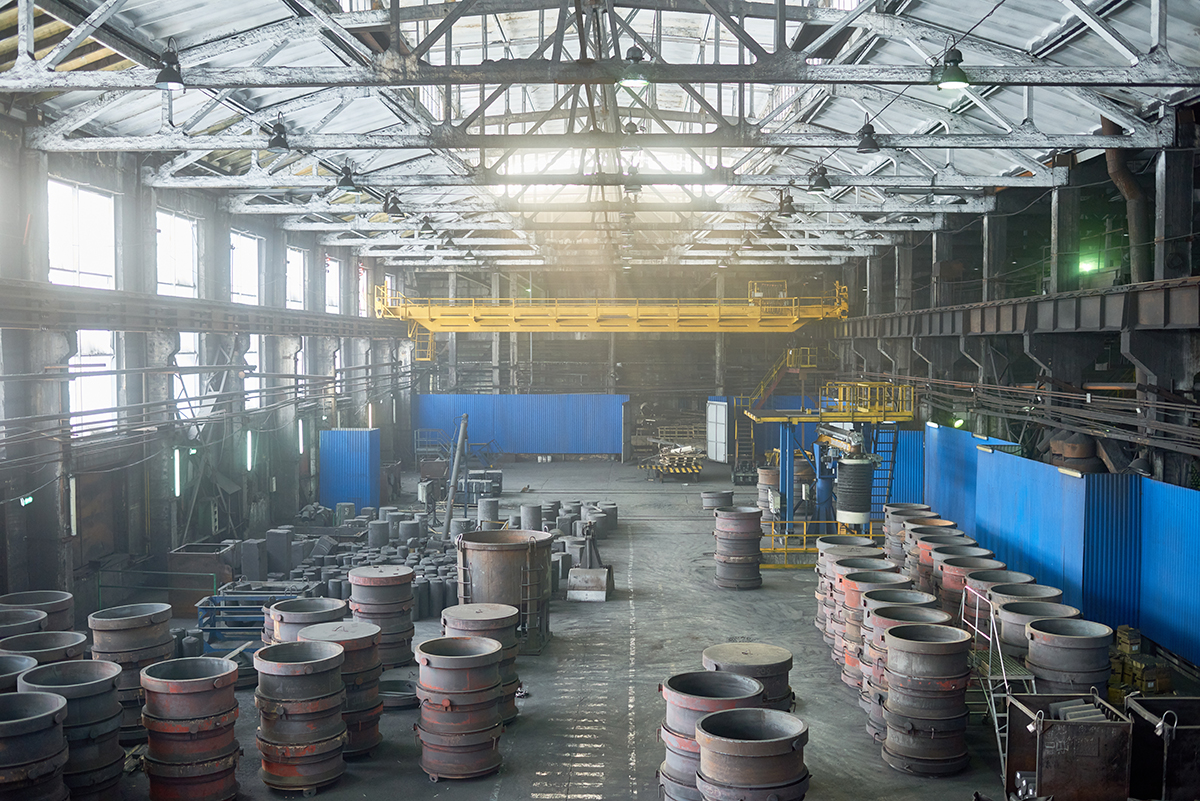
Dokonce i kdybychom měli nadbytek zakázek, dostatek výrobních kapacit, naprosto bezporuchovou technologii a trvalou disponibilitu vstupního materiálu, vždy se nějaký „waiting time“ objeví. Čím to je a jaké jsou možnosti eliminace čekacích dob?
Jak už bylo uvedeno výše, nebudeme se nyní zabývat čekáním kvůli poruchám zařízení, chybějícímu materiálu, problémům s kvalitou nebo nedostatku strojních či lidských kapacit. I když všechny právě uvedené příčiny přerušení výroby eliminujeme, přesto zůstanou tři základní typy čekání.
Typ-1: velikosti výrobních dávek. Když bude výrobní dávka stanovena na 100 kusů a každý se bude opracovávat 1 minutu, bude každý kus 99 minut čekat a to buď než na něj přijde řada nebo na zbylé kusy po něm, než bude celá výrobní dávka posunuta k dalšímu zpracování. Pouze tedy u jednokusových výrobních dávek (tzv. „one piece flow“) bude čekání nulové.
Typ-2: přestavby zařízení, před nájezdem dalšího (jiného) výrobku. Navzdory tomu, že provádění přestaveb je kvalifikovaná činnost s přidanou hodnotou, vyvolané čekání je ve výrobním prostředí velmi neoblíbené. To samozřejmě vede ke snaze navyšovat výrobní dávky s důsledkem nárůstu čekání typu-1.
Typ-3: asynchronnost výrobních procesů. Je-li konečný výrobek smontován byť jen ze dvou vyráběných komponent, nepodaří se vždy, aby byly 1:1 pro montáž k dispozici v jeden okamžik. Tím spíše je-li těchto komponent více.
Plánování a řízení materiálového toku ve výrobě tak, aby suma výše uvedených typů čekání byla minimální, může být poměrně náročnou logistickou úlohou. Nezřídka dokonce jde o pořádný rébus. Historie řešení eliminace čekacích dob ve výrobě je však již dlouhá – máme tedy k dispozici vzorové postupy „jak na to“:
- optimalizace velikosti výrobní dávky (EBQ - Economic Batch Quontity)
- zkracování přestavovacích časů (SMED Single Minute Exchange of Dies)
- aplikovaná teorie úzkých míst („synchronizovaná výroba“)
- optimalizace lay-out ve výrobě (Systematic Layout Planning)
- intralogistika (navrhování výrobních linek)
Vše to začalo koncem 19. století v USA popularizací tzv. „taylorismu“ (Frederic Winslow Taylor), rozvinulo se ve 20. století např. v Japonsku (tzv. „Toyota Production System“) a pokračuje v celém světě ve století 21. a to včetně střední Evropy – mimo jiné také na půdě Logistické akademie (viz vzdělávací modul M3 – Plánování výroby a intralogistika). Buďme vděčni osudu, že je stále se co učit 😊